

Silkscreen printing is used in many different art and design areas, such as: The most successful silkscreen prints use bold, simple shapes and designs with limited colours.

To allow the colour to flow easily through the pores and to fix the design.
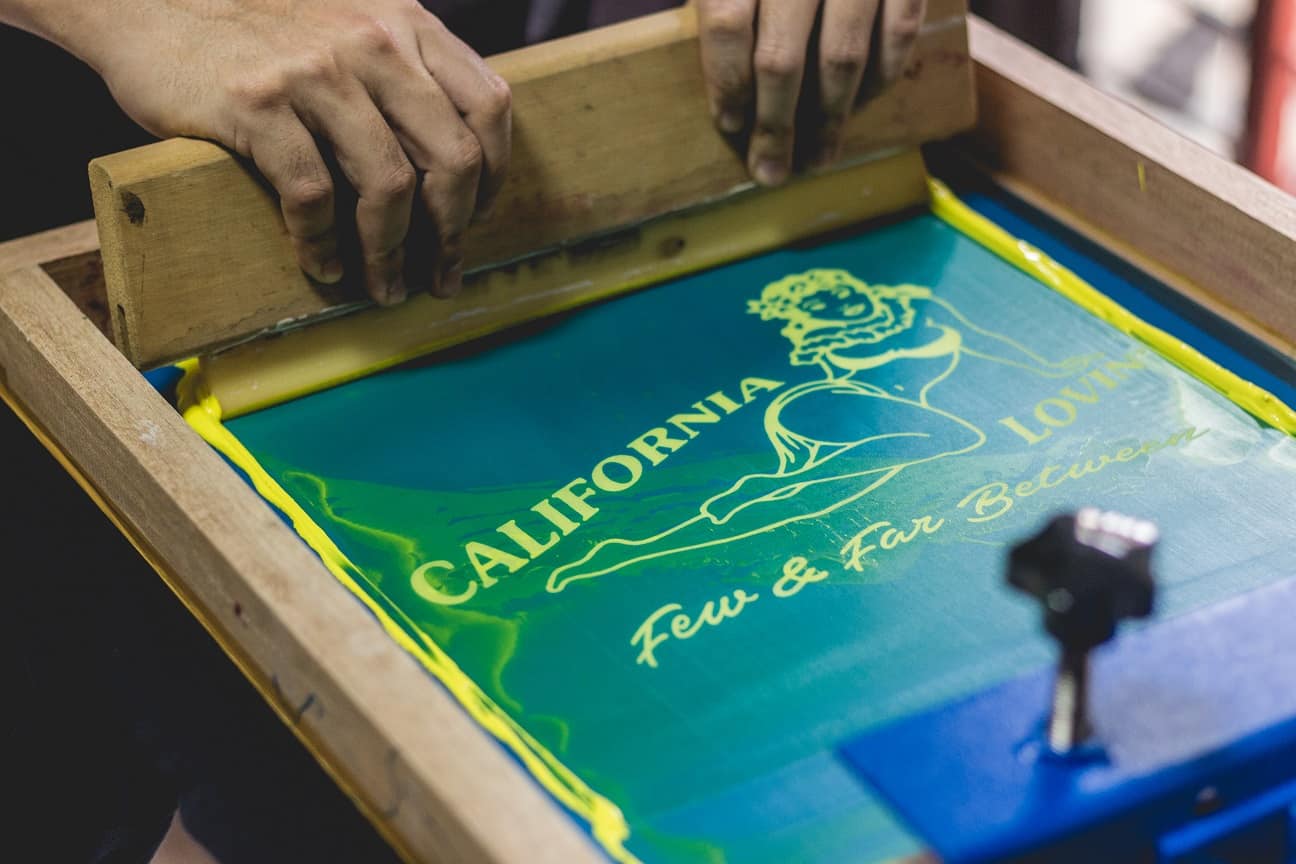
Silkscreen prints are usually made with acrylic paint that is mixed with a binder The design is printed by having a squeegeeįorce colour through the pores of the material in the areas that are not blocked out by the stencil. The screen is coated with a light-sensitive gel and the acetate image is exposed onto the screen using a ultra-violet light source. If using acetate, you photocopy your image onto an acetate sheet. Placed over a mesh cloth stretched over a heavy frame.Ī stencil can be created by carefully cutting out a design from paper and then attaching it to the silkscreen.
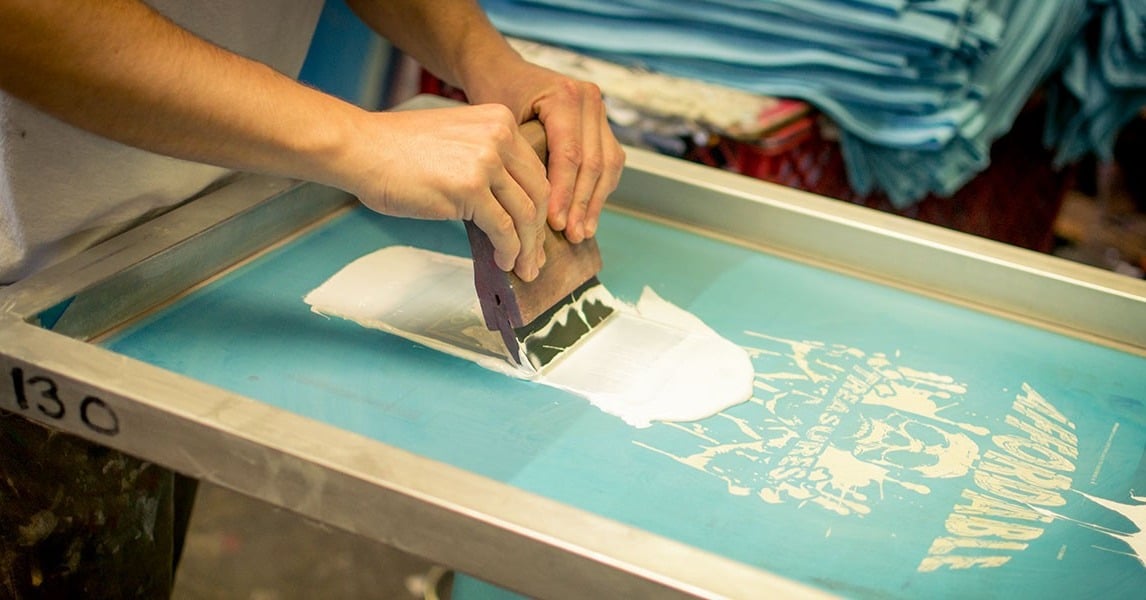
Silkscreen printing is sometimes known as the silkscreen process. The final product is checked and washed to remove any residue before going to packaging and shipment.Simple designs and bold colours work well in silkscreen prints Step 7: The printed product will now pass through the dryer, which cures the ink and makes the design look smooth. Once all items have been printed, the mesh is washed off the emulsion for another project. If the printer has to create multiple items, the screen is raised, and a new garment goes under it. The squeegee helps disperse ink to the open areas of the stencil to imprint the design. A squeegee is used to pull ink along the length of the stencil. Step 6: The screen lowers on the printing board, and ink goes on top of the mesh screen. This printer is ideal for multicolored prints as well as it can apply different layers in quick succession.
#Silkscreen printing is manual#
There are different presses, including manual and auto presses, but commercial printers mostly go with a rotary carousel printer. Step 5: The screen goes onto the printing press, and the item to be printed is placed right under the screen. The screen is then sent to dry, and any necessary touch-ups or fixes are done at this point. Now, a clear imprint of the design is visible on the mesh screen. At this point, any unhardened emulsion is carefully washed away. Step 4: After the screen spends a set time under the light, the areas not covered by design also become hard. The skill of a printer is of immense importance here because they have to create each stencil and line it perfectly to ensure that the final design is as expected. If the final design has more than one color, then a separate screen is required to apply every layer of ink. The light hardens the emulsion, and only the screen parts covered by design remain liquid. Step 3: The acetate screen with the printed design is now laid onto the mesh screen and put under a bright light. This is done to ensure the screen hardens when placed in bright light. Next, the printer uses a light-reactive emulsion to coat the mesh screen. Step 2: Next, the printer chooses a mesh screen that suits the job the most and matches the texture of the printing surface. This film plays a crucial part in creating the stencil. Step 1: The printer takes the design to be printed on the surface and prints it out to a transparent acetate film. It is also the most popular type of screen printing and is used to make intricate stencil designs. The method we will discuss requires a special emulsion to create a stencil. There are a couple of screen printing methods, but all of them involve the same printing technique.
